ОСНОВИ НА ИЗМЕРВАТЕЛНАТА ТЕХНИКА
1.ЦЕЛ И ЗНАЧЕНИЕ НА ИЗМЕРВАНИЯТА В МАШИНОСТРОЕНЕТО
Измерването е процес, при който се сравнява измерваната величина с друга, приета за единица мярка. Например измерена дължина 2 га означава, че дадената дължина е два пъти по-голяма в сравнение с международно приетата единица мярка за дължина-метър. При измерването се установява колко пъти е по-голяма или каква част представлява измерваната величина от единицата мярка.
Чрез технически измервания в машиностроенето се контролират линейните и ъгловите размери на детайлите и възлите, съставляващи отделната машина. Така се осигурява качественото изработване на машината.
Целите на техническите измервания в машиностроенето са: да се установи точността на изработваните детайли и изделия в съответствие с тяхното предназначение и да се контролира точността на технологичните процеси за предотвратяване на брака.
Техническите измервания придобиха голямо значение в съвременното машиностроене при внедряването на високопроизводителни методи на производство, механизация и автоматизация на технологичните процеси. В машиностроенето съществува тясна връзка между производството и измерванията. Чрез уредите за контрол, свързани с уредите за автоматично управление, се ръководят производствените процеси. От правилния избор на начина и средствата за контрол зависят качеството на продукцията, загубите от брак и производителността на процеса.
2.ИЗМЕРВАНИ ВЕЛИЧИНИ
Необходимостта от измерването на различни величини датира от най-дълбока древност. Мерките са се появили, за да задоволяват нуждата на човека да сравнява предмети от заобикалящата го среда. Измервани величини са: дължина, повърхнина, обем, маса и време. Дълго време мерки за дължина били аршинът, саже- нът и цолът. Това Разнообразие от мерки за дължина и тяхното непостоянство са създавали затруднения в търговията. Наложило се тези мерки да се уеднаквят и да се създаде единна международна система. Така се стигнало до установяването на двете системи: метрична и цолова.
Метричната система датира от 1791 г., когато за единица мярка за дължина е била приета една четиридесетмилионна част от дължината на Парижкия меридиан, наречена метър. След завършване на изчисленията на дължината на меридиана е бил изработен еталонен метър от платино-иридиева сплав с минимален коефициент на линейно разширение. Той представлява прът с обща дължина 1020 mm с напречно Х-образно сечение. Международният прототип не определял метъра с достатъчна точност за съвременните изисквания. Необходимо било да се приеме естествен и неразрушим еталон. През I960 г. Единадесетата генерална конференция по мерки и теглилки приема нов еталон. Метърът е дължина, равна на 1650763,73 дължини на вълната във вакуум на лъчението, отговарящо на прехода между нивата 2р10 и 5db на атома на криптон 86.
Цоловата система е приета в Англия и САЩ. В основата на тази система е цолът (1 цол е равен на 25,4 mm). В България е приета и е задължителна метричната система.
3. ТОЧНОСТ НА ИЗМЕРВАНЕТО
Основните изисквания, на които е необходимо да отговарят измерванията в машиностроенето, са точност, профилактичност и производителност. Ето защо при избора на метод за измерване се съобразяваме с тези изисквания.
Точността на измерването е условие, което осигурява получаване на предписаните размери на изработваните изделия. Тя зависи от основните показатели на измервателните уреди и инструменти. Към тези показатели се отнасят стойността на делението на скалата, точността на отчитане, границите на измерване по скалата, чувствителността на уреда, стабилността на показанията на инструмента, измервателното деление и др. Точността на измерването зависи още от квалификацията на оператора и температурния режим. Точни измервания се извършват в специални помещения, в които се поддържа постоянна температура 20° С. Към измерване се пристъпва, след като детайлите са изравнили своята температура с тази в помещението.
КОНТРОЛНО-ИЗМЕРВАТЕЛНИ ИНСТРУМЕНТИ
1. ИНСТРУМЕНТИ ЗА ИЗМЕРВАНЕ НА ЛИНЕЙНИ РАЗМЕРИ
Измервателната линия се използува за измерване на дължини. Изработва се [ от инструментална стомана с дължина до 2 метра,разграфена на сантиметри. С нея се измерва,като се поставя нулевото деление да съвпадне с единия край на предмета, и се отчита дължината по делението, което съвпада с другия му край. Ако този край не съвпада точно с някое деление, частите от милиметъра се отчитат приблизително.
Ролетката се използва за измерване на дължини до 20 м. Намира приложение най-много в строителството. Изработва се от пружинна стоманена лента. Разграфена е на метри, сантиметри и милиметри. За по-лесно пренасяне се навива върху подходящо оформен носач, кутия и др., откъдето носи и названието си.
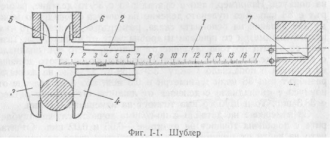
Шублерът (фиг. 1-1) е широко използван измервателен инструмент в машиностроенето. Служи за измерване на външни и вътрешни размери, дълбочини на отвори и дължини на детайли. Конструктивно той е оформен с използване на нониус —спомагателна скала за по-точно отчитане на дробни части от деленията на основната скала. С нониуса се постига точност на измерването до 0,1, 0,05 н 0,02 mm. Най-голямо приложение намират шублерите с дължина от 120 до 300 mm. Изработват се шублери с дължина до 2000, а за специални случаи и до 4000 mm.
Съставните части на шублера (фиг. 1-1) са разграфена линия / и плъзгач 2, челюсти 3 и 4 за измерване на външни размери и съответно 5 и 6 за измерване на вътрешни размери. За измерване на дълбочини на отвори служи линийката 7 към плъзгача, която се движи по обратната страна на разграфената линия. Линията е разграфена в сантиметри и милиметри. Върху скосената част на плъзгача срещу деленията на награфената линия е нанесена скалата на нониуса. Той е с дължина 9 mm и е разделен на 10 равни части. Следователно всяко деление от нониуса е равно на 0,9 mm и се различава от деленията на линията с 0,1 mm. При допрени челюсти една към друга нулевите деления на линията и нониуса съвпадат.
За да се измери даден детайл, е необходимо чрез придвижване на плъзгача челюстите на шублера да го обхванат и да се застопорят. Шублерът се снема и размерът се отчита по делението на разграфената линия, с което е съвпаднало нулевото деление на нониуса. Например, ако е съвпаднало с 38-то деление, размерът е 38 mm. Ако нулевото деление на нониуса е попаднало между две деления на основната скала, размерът се отчита, като към целите милиметри се прибави и дробна част от милиметъра. Тази част се отчита по това деление от нониуса, което е съвпаднало с едно от деленията на линията. Например, ако нулевото деление на нониуса е попаднало между 38- и 39-о деление на линията, размерът има 38 цели милиметри и 0,3 mm, ако 3-то деление от нониуса е съвпаднало с деление от линията. Отчетеният размер е 38,3 mm. Този шублер има точност на измерване 0,1 mm.
За измерване на детайли с по-голяма точност служат шублерите с повишена точност на отчитане 0,05 и 0,02 mm. Отчитането на части от милиметъра с тези шублери става по нониус с дължина за първия 39 mm, разделена на 20 равни части, а за втория 49 mm, разделена на 50 равни части (фиг. 1-2).
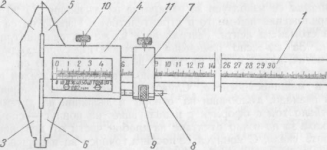
Този шублер има по-сложно устройство. Неговите съставни части са разграфена линия 1 с челюсти 2 и 3, плъзгач 4 с челюсти 5 и 6 и хомот 7. Последният е свързан с плъзгача посредством винт 8 и гайка 9. Плъзгачът и хомутът се застопоряват към линията с винтовете 10 и 11. Върху рамката на плъзгача е нанесен нониу- сът. Xомотът служи за точно нагласяване на шублера на желан размер чрез въртене на гайката 9 върху винта 8. За целта е необходимо най-напред да се застопори хомотът към линията чрез винта 11. Посредством челюстите 2 и 5 се измерват само външни размери, а с другите две —3 и 6— външни и вътрешни размери.
При измерване на вътрешни размери трябва към отчетеното показание на шублера да се прибави числото 10, тъй като всяка челюст е широка 5 mm. При плътно допрени една до друга челюсти нулевите деления на нониуса и основната скала и 50-о деление на нониуса с 49-о деление на основната скала съвпадат. Всяко деление на нониуса е равно на 49:50 = 0,98 mm и се различава от делението на линията с 0,02 mm.
На същия принцип са устроени шублерът-дълбокомер, предназначен за измерване на дълбочини, и шублерът-зъбомер, с който се измерват едновременно височината и дебелината на зъба на зъбни колела.
Шублерите се изработват от инструментална стомана. Измервателните им повърхнини се закаляват повърхностно, за да не се износят лесно.
Микрометърът се използува за измерване на външни размери с точност до 0,01 mm. Изработват се микрометри за измерване на размери от 0,01 до 1600 mm. Обхватът на измерване с един инструмент е 25 mm.
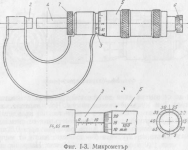
Микрометърът (фиг. 1-3) се състои от скоба 1, пета 2, вътрешна втулка 3, микрометричен винт 4, външна втулка 5, тресчотка 6 и застопоряващо устройство 7. Върху стеблото 3 надлъжно е нанесена скала с деления в милиметри (през 0,5 mm). Върху конусната
част на външната втулка 5 е нанесена кръгова скала с 50 равни деления за отчитане на дробни части от милиметъра. При един оборот на външната втулка 5 микрометричният винт се премества на 0,5 mm, а при завъртане само на едно деление по кръговата
0 5
скала винтът ще се премести на =0,01 mm.
За да се измери един детайл, той трябва да се постави между петата 2 и микрометричния винт 4. Чрез въртене на втулката 5 и тресчотката 6 винтът се допира плътно към детайла и се застопорява с устройството 7. Микрометърът се снема и върху скалата-'на стеблото 3 се отчита размерът през 0,5 mm, а по кръговата скала на втулката 5 дробните части от милиметъра
през 0,01 mm. Например по линейната скала е отчетена дължина 28,5 mm, а по кръговата 0,28 mm. Тогава размерът ще бъде равен на 28,78 mm.
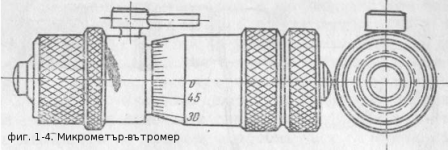
Други видове микрометри са микрометър-вътромер, микроме- тър-дълбокомер и микрометър- резбомер.
Микрометърът-вътромер (фиг. 1-4) има същото принципно устройство, както обикновеният микрометър. Конструктивно той е оформен без стоманена скоба. С него се измерват отвори с диаметър над 30 mm. По-големи размери се измерват, като към него се завинтва удължител с точно определена дължина. Към отчетения размер по скалата на инструмента се прибавя дължината на удължителя. Точността на измерване с микрометър-вътромер е 0,01 mm.

Микрометърът-дълбокомер (фиг. 1-5) се състои от опора /, съединена неподвижно с вътрешната втулка 2, в която се движи стеблото 3 на микрометричния винт, и застопоряващото устройство 4.
За измерване на големи дълбочини се използуват удължители на стеблото с точно определена дължина. Последната трябва да се прибавя към отчетения размер.
Макрометърът-резбомер (фиг. 1-6) се използува за измерва-
не на средни и вътрешни диаметри на външни резби. За всеки вид резба се използуват сменяеми накрайници / и 2, които се поставят в отвора на петата 3 и стеблото 4 на микрометричния винт. Този микрометър се настройва на нула чрез преместване на петата 3 посредством втулка 5. Накрайниците за измерване на съответен вид резба се застопоряват с устройство 6 и 7. Точността на измерване и при този микрометър е 0,01 mm.
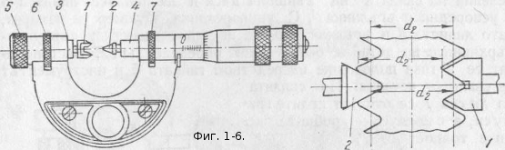
Следва продължение...........................
Last edited: